Pedestal Ram Luffing Offshore Crane
After one decade of loyal service this crane is for sale.
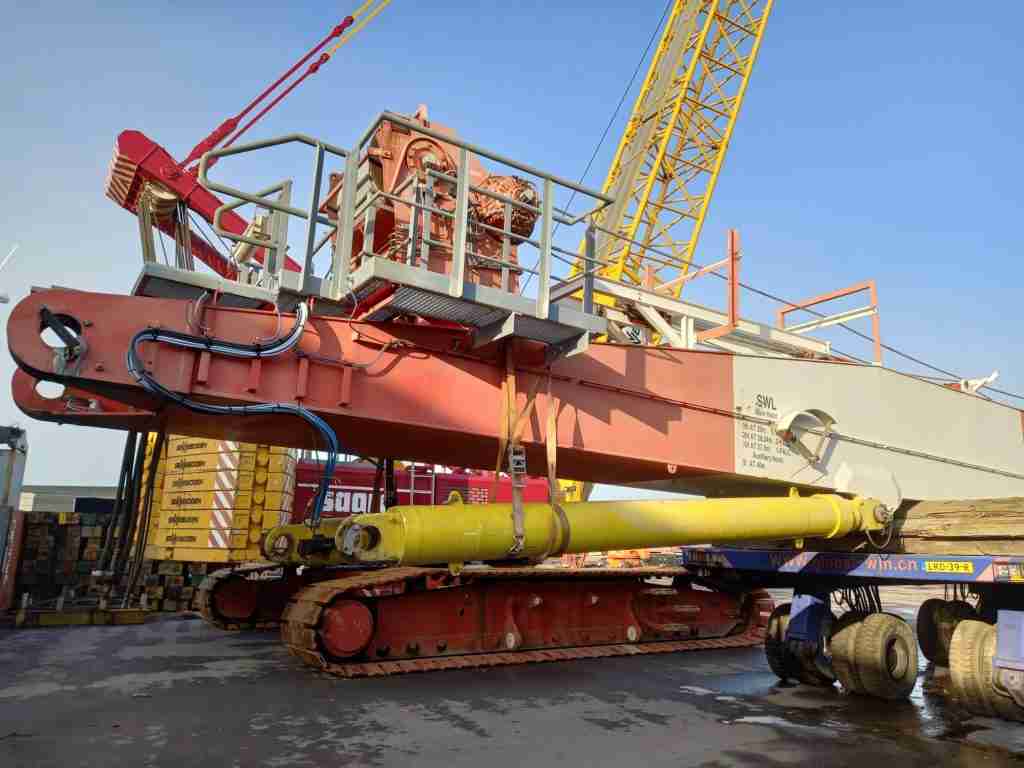
Request more information
This DHC 30/3000 O.S. RL is a Ram Luffing (RL) offshore crane which employs hydraulic power for its main functions – Hoisting, Slewing and Luffing. This Diesel Hydraulic version with a slewbearing diameter of 3000mm is of this size in Kenz’ standard offshore crane range, specifically designed for use on fixed offshore platform installation. This crane is optimised for small to medium day-to day lifts at moderate radius, specifically suitable offshore production platforms and/or offshore substations.
Kenz Ram Luffing cranes are designed for limited maintenance intervals and offer a very low total cost of ownership for cranes
that are not used with high intensity. The crane contain first class West European components and equipment.
This Kenz Ram Luffing (RL) offshore crane was designed according to Lloyd’s Code for Lifting Appliances in a Marine Environment 2009
and supplied with 3rd party Lloyd’s Register of Shipping design certificate (Design Approval Document).
The crane is manufactured in 2010 at Kenz premises in The Netherlands and installed on the F3-FA production platform. After
one decade of loyal service this crane is for sale
Lifting capacity
Main hoist | Platform | 3-falls – max SWL=30t | 30t @ 20m and 14t @ 37,5m | ||||
Supply boat – SWH=0,6m | 3-falls – max SWL=30t | 30t @ 10m and 11t @ 37,5m | |||||
Supply boat – SWH=3,9m | 2-falls – max SWL=20t | 20t @ 10m and 6t @ 37,5m | |||||
Constant Tensioning Main hoist | 0-4t @ 120 m/min 1-fall | ||||||
Auxiliary hoist | Platform | 1-fall – max SWL=5t | 5t @ 40m | ||||
Supply boat – SWH=3,9m | 1-fall – max SWL=5t | 5t @ 40m | |||||
FRC handling – SWH=3,0m | 1-fall – max SWL=4t | 4t @ 40m | |||||
Constant Tensioning Aux. hoist | 0-4t @ 120 m/min 1-fall | ||||||
Hook speeds | Variable load dependent speed, step-less from zero to maximum SWL | ||||||
Main hoist | 0-15 m/min (3-falls with 30t) 0-30 m/min (3-falls with 0t) | ||||||
Auxiliary hoist | 0-120 m/min (1-fall with 5t) 0-120 m/min (1-fall with 0t) | ||||||
Slewing | Double row ball-bearing with internal gear teeth | ||||||
Slewing range | Unlimited (n x 3600) due to Slipring body (EX rated) | ||||||
Slewing speed | 0-1.0 rpm | ||||||
Luffing | Two (2) double-acting cylinders | ||||||
Luffing time full load | Approx. 100 sec. max to min radius | ||||||
Main hoist range | 6,6m – 37,5m | ||||||
Auxiliary hoist range | 7,5m – 40m | ||||||
Modes of operation | Deck lift Operations | ||||||
Supply boat Operations | |||||||
FRC Handling |
Design Criteria
Main design code | LAME 2009 | ||||||
Ambient working Temperature | -10° C up to +26° C | ||||||
Design wind speeds | 20 m/s and 63 m/s stored | ||||||
Structural Design life | 30 years | ||||||
Crane Duty-Cycle Classification | According NEN 2018 | ||||||
Class of Utilization | B | ||||||
State of loading | 1 from main hoist and 3 for aux hoist | ||||||
Group classification for Crane | 3 from main hoist and 5 for aux hoist | ||||||
Classification of Mechanisms: | Main hoist Aux hoist Luffing Slewing | ||||||
Duration of use | T3 T4 | T4 | T4 | ||||
Spectrum class | L3 L3 | L2 | L2 | ||||
Group classification for Mechanism | M4 M5 | M4 | M4 | ||||
Hazardous Area Classification | Crane | ||||||
Zone | Zone 2 | ||||||
Class | IIA | ||||||
Temperature Class | T3 |
Interface Data
Nominal Weight | |||||||
Crane gross wet weight | 78t | ||||||
Pedestal adapter (tapered) | 4.5t (1600mm height, interface ø2542mm) | ||||||
Dynamic overturning moment | (at slewbearing level, +/- 10%) | ||||||
Max. Dyn. Overturning moment | 12400 kNm | ||||||
Max. Dyn. Axial Force | 1120 kN | ||||||
Max. Dyn. Radial Force | 50 kN | ||||||
Max. Dyn. Slewing Moment | 475 kNm | ||||||
Power Unit | Main driver | ||||||
Main power (DHC) | Caterpillar 3406 DI-TA four stroke Diesel engine with exhaust muffler and spark arrestor (Zone 2) |
Outfitting
Preservation / paint acc | Ameron International Sa 2 1/2 according to ISO 8501-1 | ||||||||||||||
Layer | Min. DFT (µm) | System | |||||||||||||
Layer 1 | 75 | Dimetcote 9, inorganic zinc silicate | |||||||||||||
Layer 2 | 40 | Amercoat 71 TC, epoxy tiecoat | |||||||||||||
Layer 3 | 125 | PSX 700, epoxy polysiloxane topcoat | |||||||||||||
Total | 240 | ||||||||||||||
Failure philosophy | Cabin support structure will be the last to fail | ||||||||||||||
Mechanical | Fail safe spring loaded hydr. released parking brake on primary shaft of winch drive gear box and slewing gear box | ||||||||||||||
Emergency shut-off valve in engine air inlet and fuel governor, initiated only by Diesel overspeed, low-booster pressure or emergency stop push-button application | |||||||||||||||
Main Hoist Hook catcher | |||||||||||||||
100% RotaBolts at inner and outer slewbearing | |||||||||||||||
Hydraulic | Full size pressure relief valves in all systems | ||||||||||||||
Hydraulic lock valves directly on winch motors | |||||||||||||||
| |||||||||||||||
Electric | Control power batteries back-up for 30 min of autonomous working | ||||||||||||||
Emergency stop push button in cabin | |||||||||||||||
Interlock to allow starting only with all function in neutral | |||||||||||||||
Limit switches on hoists for extreme hook positions | |||||||||||||||
Luffing-down cut-out at 110% of permissible load moment (reverse possible) | |||||||||||||||
Aircraft Warning Light at top of boom, Warning horn to deck crew operated by push button, Temperature monitoring on boom | |||||||||||||||
Automatic & Manual Overload Protection System | Manually activated winch brake release and rope pay-out under back tension incl. last windings limit override and break-away rope link to the winch drum | ||||||||||||||
Manual emergency operation | Lowering of the hook, Boom lowering by opening a ball value, Emergency slewing brake release (slewing by external force) | ||||||||||||||
Powered emergency operation | By means of separate E-motor and selector valves, Emergency lowering of hooks and boom, Emergency slewing, Emergency hoisting AH and luffing up 5t | ||||||||||||||
Maintenance | Suitable foundation with removable service crane | ||||||||||||||
Water tight hatch in mainframe | |||||||||||||||
Walkway near winch and left side along the complete boom |
